The Automatic Testing Machine for testing of Inverter/UPS, Solar inverters
The RnD team of Su-vastika develops an automatic testing machine for testing inverter/UPS. We created this Machine to test our products and parameters, which we feel is essential for us to try as we need continuous up-gradation of these parameters. We are developing a new range of products in power backup and storage solutions with Solar and Lithium battery. We have an Automatic battery inverter/UPS/Solar PCU/ Battery Energy Storage Systems/Lift Inverters testing system of Su-vastika.
We use the Power Analyzer to test all of our parameters that are tested in our various models of the inverter, UPS, and online UPS. Solar Inverters. Solar PCU. Heavy Duty UPS and battery Energy Storage Systems and Lift Inverters. We have different software to test those parameters for a diverse range of products. So, for example, we try our Pure Sinewave UPS with an ATC model on Automatic Testing Machine for which we have these parameters to select.https://suvastika.com/how-automatic-testing-solutions-pave-the-path-to-success/

Inverter Testing Tool’s Display
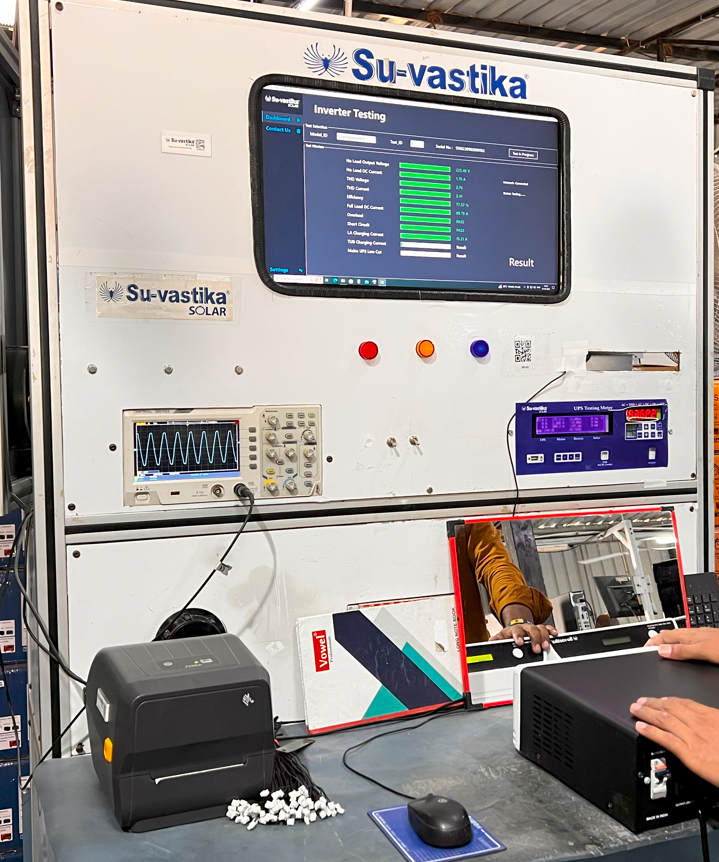
We have these critical parameters that are the Automatic battery Inverter/UPS Testing system tested on this machine. These parameters are:
No Load Output Voltage
No LOad DC Current
THD Voltage
THD Current
Efficiency
Full load DC Current
Overload
LA charging Current
Tubular charging current
Mains UPS Low Cut voltage
We read the values of these parameters through the Power Analyser installed in this Machine, and we have preset the parameters of each model into the system. When we select this product model, all the parameters fed into the system come on the screen. The operator clicks the screen Tesrt button, and the Machine starts testing these parameters individually. It takes almost two minutes to try the operator, and all these parameters are tested along with the values. Once tested, the Printer prints out the sticker creating the automatic QR code sticker having the serial no generated automatically. This QR code has a lot of information and the serial no of the product. After testing, the operator takes the sticker and sticks it on the back of the product, and four stickers are printed, which can be placed in various places such as on the packaging box and warranty card, etc.https://www.mitsubishicritical.com/services/testing/



Once the product is tested, the data of each product goes on the cloud server AWS for which we have a dedicated application software with AI. This cloud-based software stores the data of each product, and we have a lot of analytics built into this software which can tell us about the operator efficiency and the product failure data; the repeated problems in the testing and complete traceability are maintained.

If a product fails, the data and serial number are kept. If the product fails in testing, the serial number is created, and the failed items are printed on the sticker, which helps our repair department to recheck these areas. After repair, the product is tested with the same serial number, and this data is stored in our cloud server for future traceability. All these cloud data are merged with our CRM server for customer traceability along with this data. We have already filed the technology patent for this Testing machine in the Indian Patent Office.
Under the Make in India campaign, we can compete with China regarding technology and price.https://suvastika.com/new-automatic-testing-machine-for-inverter-ups-ensures-safety-accuracy-and-reliability/
Here are some of the benefits of using an Automatic battery Inverter/UPS Testing System
We don’t need trained engineers to test the products
Increased accuracy and repeatability of test results
Reduced test time
Increased safety for technicians
Traceability on a digital cloud server
The QC Engineer required so no manual intervention
The Printer helps in output data display.
Usually I never comment on blogs but your article is so convincing that I never stop myself to say something about it. Really helpful.